
Medical Division
(Medical Device Business)
The Medical Division aims to establish the medical device business through collaboration with various related organizations, including joint research with university hospitals. We are looking for people with an interest in medical devices, ambition, and energy, regardless of experience in medical device development.
Interviews
Department of Orthopaedic Surgery, Shimane University School of Medicine
The concept of a multifunctional bone processing machine was born from the research that had been conducted by the Department of Orthopaedic Surgery, Shimane University School of Medicine. At the root of this concept is a sense of mission as a clinician to help patients. We asked the researchers who have been engaged in research and development for many years about their reasons for starting their research and their future plans.
Overcoming difficult-to-treat cases with technological innovation that “heals bones with bones”
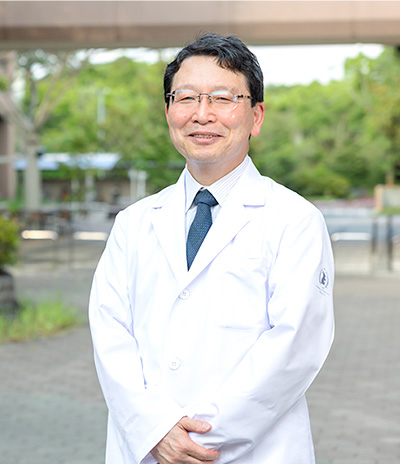
Yuji Uchio, MD, PhD.,
PROFILE
Professor, Department of Orthopaedic Surgery, Shimane University School of Medicine Specializing in knee joint surgery, Dr. Uchio has performed surgery for more than 3,000 patients to date. He belongs to many academic societies, such as the Japanese Orthopaedic Society, Japanese Knee Society, Central Japan Association of Orthopaedic Surgery & Traumatology, Japanese Society for Surgery of the Hand, Chugoku-Shikoku Orthopaedic Association, Japanese Orthopaedic Society of Knee, Arthroscopy and Sports Medicine (JOSKAS), Japanese Society for Joint Diseases, and Japanese Orthopaedic Society for Sports Medicine (JOSSM). He has also published numerous papers in his area of expertise.
Research began with inspiration from wood joinery used by shrine carpenters
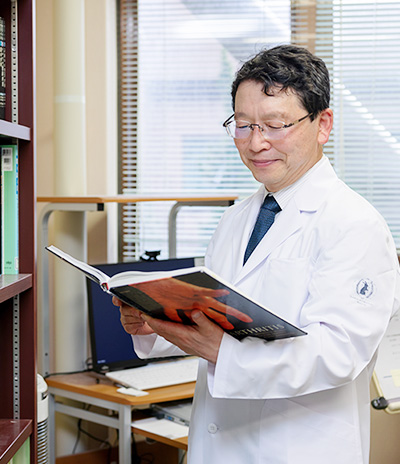
Shrines and temples that have been around for centuries in Japan were built using the technique called Kigumi, wood joinery, of miyadaiku (specialists in construction of shrines and temples). Despite not using a single nail, these wooden structures are extremely durable, and some structures still exist that are hundreds of years old. My research began with the idea that this technology could be applied to fracture treatment. This is an attempt to “heal bones with bones,'' in a similar way to building shrines and temples using the wood joinery technique.
Fracture surgery generally involves fixing the bone with metal screws or plates. If these screws could be made from bone taken from the patient, foreign body reaction would not occur, and no surgery would be needed to remove the implanted screws. Furthermore, human bones contain components called bone morphogenetic proteins that promote bone formation, which not only act as screws but also promote bone regeneration and speed up healing. We began researching this subject in 2002, thinking that it would be a treatment that would greatly benefit patients.
We developed a machine that can process bones in 3D inside the operating room
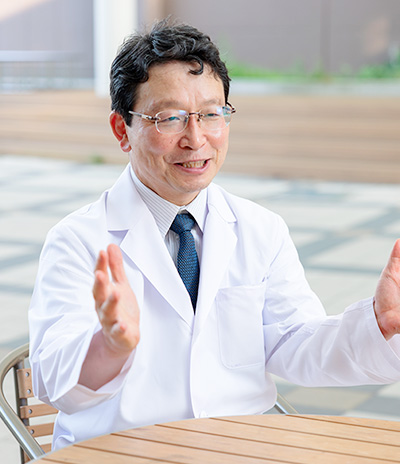
The key to this research was the development of a multifunctional bone processing machine that processes bone with high precision to form screws. Initially, we tried to make screws by modifying an industrial NC lathe and turning the bone like a potter's wheel to carve out screws, but this method had limitations in accuracy. Furthermore, due to the characteristics of bone, there was also the issue that it broke during processing. Since the patient's own bone is used in clinical practice, failure is not an option.
What we were looking for was a new machine that could cut from various directions, vertically, horizontally, and diagonally, while preventing the axis from wobbling, and that could be used in the clean environment of an operating room. Nissin Manufacturing was the one who stepped up to meet this difficult request.
It has been about 10 years since the collaboration started. Until now, we have overcome various challenges one by one, such as safety and processing speed. We believe that the latest prototype is a multifunctional bone processing machine with excellent operability that can automatically form bone screws with high precision and safety using 3D coordinate axes.
Possibility of the machine spreading from Japan to the world

If this processing machine is used in medical settings, it can be applied not only to fracture treatment but also to surgeries that require bone grafting, such as ligament reconstruction and meniscus lesions. Furthermore, by combining not only the patient's own bone but also other biomaterials and metallic materials, it will become possible to perform effective surgeries that maximize the advantages of each material.
Currently, we create a program for each case to control the cut shape of the bone, but in the future we would like to further develop a system that can automatically generate programs using X-rays, CT images, etc. to create bone screws. If this can be done, bone screws can be made from the images sent and can be delivered in sterile packs, even over long distances. In Europe and the United States, bone banks that provide bone for transplantation are already a viable business. By adding the new value of bone screw processing to the business, we can meet a wider range of needs. I feel that the opportunities for use are endless.
To realize a society where everyone can enjoy excellent treatment
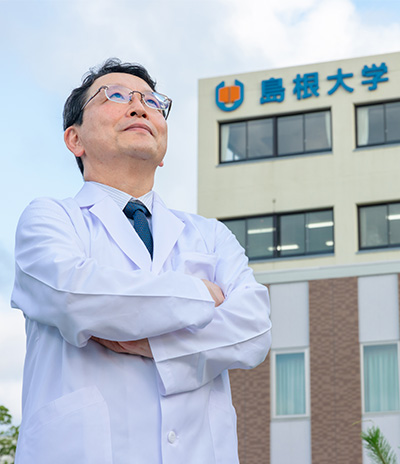
The reason I started researching bone screws was because I wanted to help a patient in need in front of me. I always thought that if such a machine were available, wounds would heal more smoothly, and patients could return to society more quickly. I believe that the mission of clinicians at university hospitals is to understand the complaints of patients and the needs of the clinical environment, study cases that are difficult to cure with current technology, and overcome those issues through technological innovation.
Our goal is ubiquitous medical care. In other words, it is medical care that can achieve a certain level of results for anyone, anywhere. We use the power of IT to cover technology gaps so that anyone can provide a certain level of treatment, rather than relying on the skills of a single expert doctor. If this becomes a reality, many more people will be able to receive an excellent level of treatment provided by top doctors. We would like to bring this technology to medical sites as soon as possible and contribute to patients who are currently in need. With this belief in mind, we will continue our research and development.
Taking a stab at the realm of craftsmanship
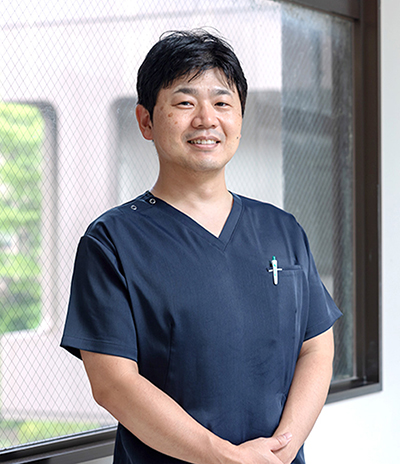
Shinji Imade, MD, PhD.,
PROFILE
Assistant Professorin the Department of Orthopaedic Surgery, Shimane University School of Medicine Member of the Japanese Orthopaedic Society and the Japanese Society for Surgery of the Foot After graduating from the Graduate School of Medical Research, Shimane University, he worked at hospitals in Shimane Prefecture, and since 2010 he has been working in the Department of Orthopaedic Surgery, Shimane University Hospital. Specializing in foot orthopaedics, he has published numerous papers.
He has been working on this project since 2007, when he was a graduate student. Since 2013, he has been playing a central role in the development of a multifunctional bone processing machine, including its clinical applications, and is taking on the challenge of developing new technologies through the fusion of medicine and precision engineering.
Contributing to bone treatment with bone screws of high processing accuracy
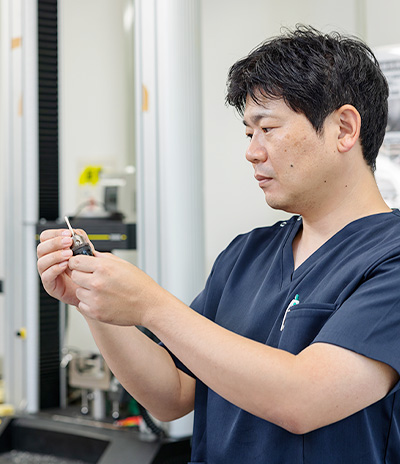
In the treatment of fractures, it is said that the postoperative course will be better if the gap between the bones is made as narrow as possible, for example to the size of a hair, when joining the bones together. Depending on the case, bone may be harvested from the patient's pelvis, processed manually, and then transplanted to the affected area. In such a case, however, the bone processing accuracy varies according to the skills and senses of the surgeon. This has led to the problem that we are unable to ensure in all cases that the gap between the bones is as narrow as the size of a hair.
One of the aims of this project is to improve machining accuracy and treatment results by replacing the manual work with a solution using a multifunctional bone processing machine. Meanwhile, in ligament reconstruction, it is currently common to implant screws made of metal or artificial materials. If these screws are made from bone taken from the patient, there will also be benefits, such as that foreign body reactions are less likely to occur and there is no need for subsequent screw removal surgery. We believe that this method can be applied to bone grafting in special cases and ligament reconstruction in sports medicine, bringing innovation to fracture treatment and bone grafting.
A new prototype completed, overcoming the barrier for medical-engineering cooperation
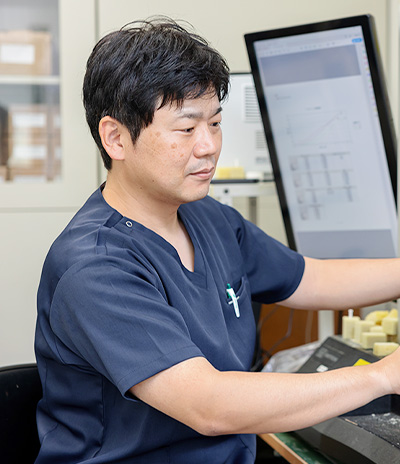
When I joined this project, a prototype machine based on an industrial NC lathe had already been completed. However, in order to create safer and more precise bone screws, a new processing machine capable of multi-axis machining was needed. Accordingly, we began developing a new type of processing machine in collaboration with Nissin Manufacturing.
Since this was medical-engineering cooperation between completely different fields, it took a considerable amount of time to develop mutual understanding. For example, we consider “accuracy” to be within a range of around 1 mm, but in the industrial field, they pursue accuracy down to tens of microns. On the other hand, when it comes to "cleanliness," we aim for a sterile state that differs from the general concept of cleanliness, and our requirements are higher. As I repeatedly communicated with people of Nissin Manufacturing, I found that the most difficult thing was bridging the gap between our understanding. However, we believe that our efforts have paid off, and the latest prototype has achieved the precision and safety that we were looking for.
I want to contribute to a wide range of treatments, focusing on sports medicine
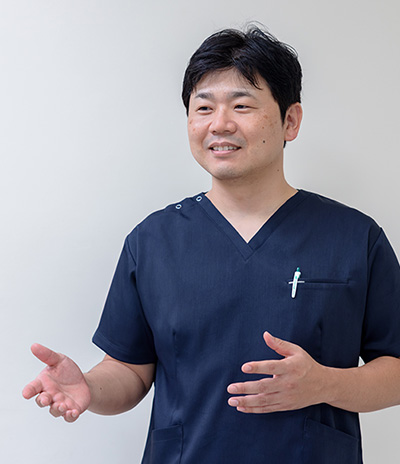
In clinical practice, we have so far performed two surgeries using a new multifunctional bone processing machine, and the patients have made favorable progress after the surgery. Both cases were very special, but anyone who has been an orthopaedic surgeon for many years comes across such rare cases at least once or twice. Up until now, we have managed to perform such a surgery manually through struggles and worries. Nevertheless, this time we were able to create bone grafts that fit the bone defect with extremely high accuracy by using the processing machine.
From now on, I would like to first focus on applying this technology to ligament reconstruction using implanted screws and develop more cases in sports medicine. In the further future, it may be possible to ensure more effective regenerative medicine in environments where foreign body reactions are less likely to occur, for example, by combining this technology with cell therapy. Also, since it is highly versatile, we hope that new developments will emerge as it is used by a variety of users.
Maximizing the performance of materials
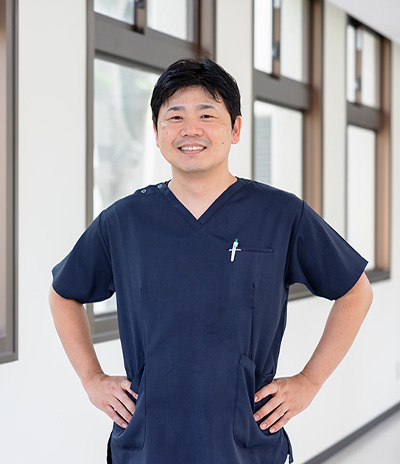
In the field of orthopaedics, it is common for surgeons to process materials by hand, and there are aspects of medical technology that rely on craftsmanship. However, in the current situation where the processing accuracy of materials depends on the skill of the surgeon, no matter how good the material is, it is not possible to make the most of its performance. By introducing a medical devicee to achieve stable processing accuracy, it is possible to maximize the performance of the material and improve the base of treatment accuracy. I think this multifunctional bone processing machine will become a medical device that changes our perception that bone should be processed manually.
In the future, it is expected that robotization will increase even more in medical care. At that time, it would be great if this machine could carry the core technology of processing materials with high precision to create a good surgical environment. The new prototype machine has significantly improved usability, increasing the benefits not only for patients but also for surgeons. I can't wait to bring this technology to the world.
Nissin FULFIL Osaka Office
The engineers in the Medical Division are currently working hard to develop a medical device in a new field. How do they face this difficult problem and overcome it? We asked two members who are active at the forefront of development about their thoughts on and the significance of the development of medical devices.
Creating medical devices that bring joy to patients

PROFILE
In her previous job, she was involved in website creation as a programmer. However, she decided to change her job because she wanted to work in a job related to the development of medical devices, which she had longed for since she was in junior high school. After joining Nissin FULFIL with no experience, she has been working on mechanism and structural design while studying from scratch.
The roots of what I do now stem from a scene I saw at a hospital
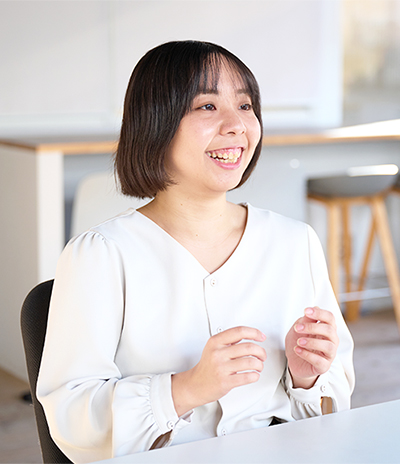
I first became interested in medical devices when I was in junior high school. At the hospital where my mother was hospitalized, I learned that various medical devices such as ventilators supported the lives of patients. This experience led me to want to create machines that could help people.
In my previous job, I worked as a programmer creating websites, but my desire to work in the medical field grew and I decided to change jobs. I had no experience in developing machines. Generally, most companies want to hire people with experience. Amid such circumstances, Nissin FULFIL was the only company that accepted me, advising me, “As long as you have a desire to learn, you’ll be fine.” During the interview, I learned that the company was working on developing new equipment that did not yet exist in the world. This made me feel that it had an environment where I could take on challenges. I was a little uneasy, but as I listened to the explanation, my desire to take on the challenge outweighed my fear. So, I decided to take the plunge and join the company.
Every day I experience the depth of parts design
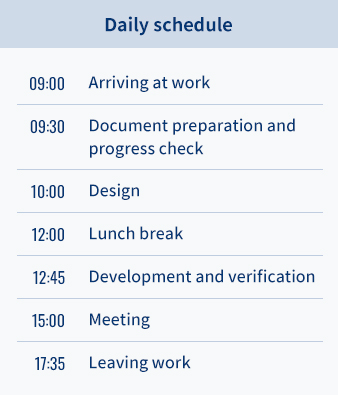
After joining the company, I was asked which field of medical device development was the focus of my interest. Because I had always liked assembling and disassembling machines, I answered that I would like to engage in mechanism/structural design. Unlike the programming I did in my previous job, this is an area in which I have no experience. However, they allowed me to take on the challenge, and I am currently involved in designing, assembling, and verifying parts.
After entering the company, a senior colleague taught me how to use CAD from the beginning. I started by modifying existing drawings, and now I’m in charge of the material selection and design of some parts of the machines. In designing medical devices, we must also take into account factors such as ease of cleaning and sterilization after use, and risks during power outages, in addition to ensuring that the parts function as intended and can be assembled safely. I am acutely aware of this difficulty, but at the same time I am increasingly fascinated by the depth of design.
I tried again and again with the support of my seniors
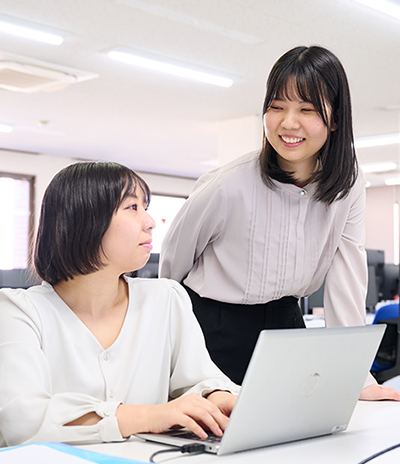
In the Development Section, there are seniors and superiors who have experience in developing various parts, such as automobile parts and air conditioning equipment parts. Therefore, I consult them and receive hints when I have a problem. The words that left the greatest impression on me were, “It’s important not to lose sight of the purpose for which we are making the parts.” After listening to these words, I always keep in mind that I should come back to the purpose whenever I start thinking too much and feel lost.
During verification, things rarely go as planned, and I often feel discouraged. Still, after going through all the trouble and making many revisions, I feel a great sense of accomplishment when I finally create something just the way I wanted it. At such times, I feel glad that I chose this job. Immediately after joining the company, I was worried about whether I would be able to make it in this job. Now, however, I feel positive with my improved motivation, hoping to be like my seniors.
I want to improve my technical skills through diverse experiences
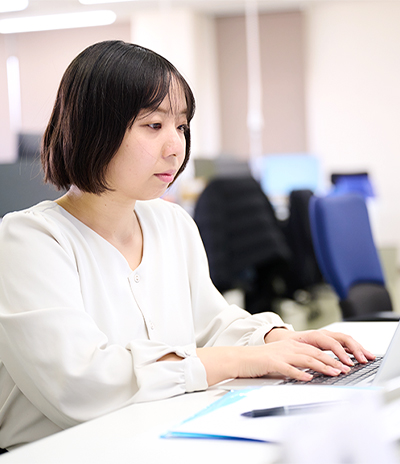
Since joining this company, I have been able to think for myself a lot more. We have to find a way to bring our device to market through various efforts, such as choosing materials that are appropriate for medical devices and solving many problems. These efforts make me feel that I am creating, with my own hands, some part for a medical device that brings joy to patients.
Now, I think it is most important for me to gain as much experience as possible. Taking advantage of the environment that provides me with opportunities to take on challenges, I want to try creating a variety of designs; to learn a lot from advice from experienced seniors and the 3D models and blueprints accumulated at our company; and thereby to generate many new ideas. Someday, I would like to acquire the technical ability to design major parts such as drive units. Furthermore, I hope to be able to play a leading role in developing business in new fields.
Making the dream of saving people with medical devices a reality
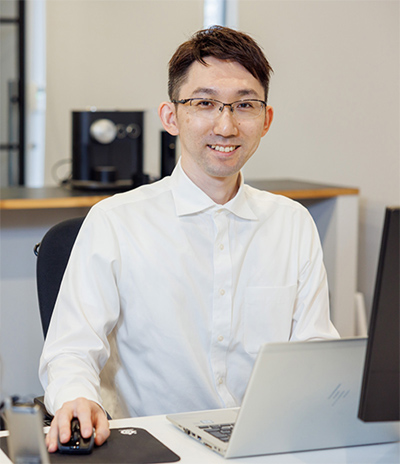
PROFILE
He joined Nissin Manufacturing in 2019. Utilizing the experience in software development for amusement machines in his previous job, he moved to the medical device industry, in which he had no experience. He has been responsible for software design and development of a multifunctional bone processing machine. Since April 2022, he has also managed the team as its chief. He is a good father who serves home-cooked meals to his family on weekends.
Challenging a new field
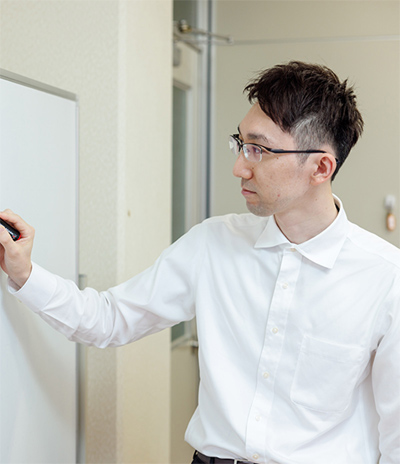
On the development team for a multifunctional bone processing machine, I am in charge of developing software related to machine control and the user interface, including screen display and button operations. We are pushing forward with development based on precision processing technology, which is Nissin Manufacturing’s strength, to further evolve the technology. So, every day is full of learning and stimulation for me. When I bring a design proposal to the table for discussion, the development team members will actively exchange opinions. There are moments when I gain a perspective that I didn't have before and come up with a new idea, saying, “Now I see what you mean!” I feel that I am gradually acquiring new knowledge and techniques by taking on the challenge of developing a medical device, in a field I had no experience in, alongside people with experience in such development.
Currently, as the chief of the team, I am also responsible for management tasks, such as managing project progress and allocating work to members. Respecting the development styles of each member, I strive to create a flexible environment where everyone can work freely.
Our sense of mission becomes stronger as the development phase progresses
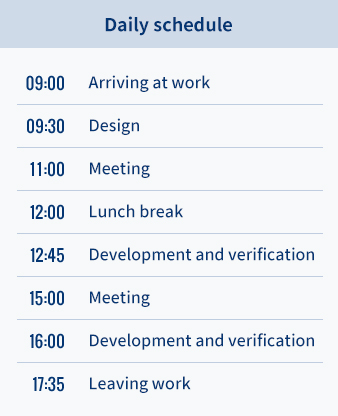
My previous job was also as a mechanical software engineer, but what is definitely different is that the equipment I am developing now is for medical use, and I am making things that are related to people's lives. We need to proceed with development in accordance with the standards without making any mistakes, rather than making vague judgments such as "it's probably possible." Ensuring that reliable numbers are produced during the prototype stage, we continue to refine our products to the point where they can be used without problems in clinical practice. It is a difficult field that cannot be conquered overnight as it requires a certain amount of medical knowledge.
However, once the product is released, the degree of perfection of the machine will be clearly seen as a result of the treatment, which gives us a great sense of achievement. This is what is great about being involved in medical device development. The further the development phase progresses, the more we realize that we want to help patients. We want to help solve the problems faced by patients with our own hands. We are feeling a growing sense of mission among our team.
Manufacturing that greatly changes the world
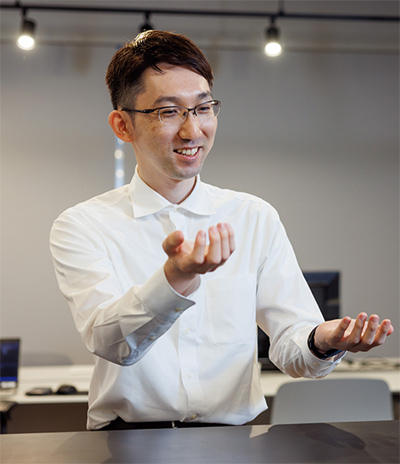
A multifunctional bone processing machine is a medical device in a new medical field. Therefore, during the development stage, we encounter various challenges that we have never experienced before. Even if we search for a solution, we often cannot find the answer from existing materials, so we have to solve the problem through repeated trial and error. Sometimes we have discussions that transcend the boundaries between software, mechanical, and electrical teams.
There are many challenges to overcome. Nevertheless, if we believe that we are taking on the challenge of creating something that has the potential to make a big difference in the world, we will be highly motivated to move forward. It is a thrilling moment when we integrate software into a machine that the mechanical and electrical teams have produced and when the prototype works as designed with all the elements working together.
Achieving a world first through the power of the team
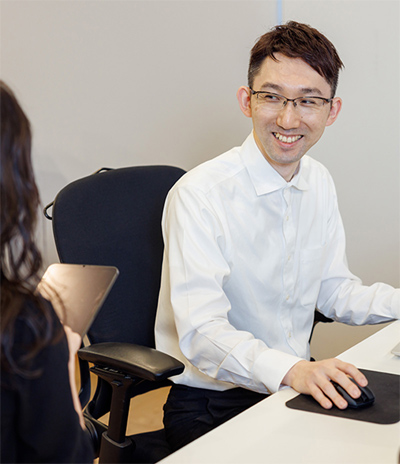
The project has entered the prototyping stage, and the future of this medical device being useful in clinical practice is becoming a reality at last. I am honored and humbled by the fact that I am helping to make that future a reality. The morale of the members is increasing. While building prototypes, we often have an active discussion on issues such as “Let's realize this point next time.” Each member has a different field of specialization, but the goal is the same: to realize the world's first medical technology and save people. I think that's why we are able to exchange opinions constructively and move forward even when the future is uncertain.
In order to keep this momentum going, I want to support the members while increasing my knowledge and continuing to grow. We will connect individual strengths to the output of the entire team and further accelerate development.
Career Plans
In the Medical Division, we support self-improvement based on a career plan. We would like to provide employees who are willing to work hard with opportunities to pursue self-actualization and support such efforts.
The chart below shows an example of a career plan. We will work together to come up with a plan that suits each person's experience and ability.
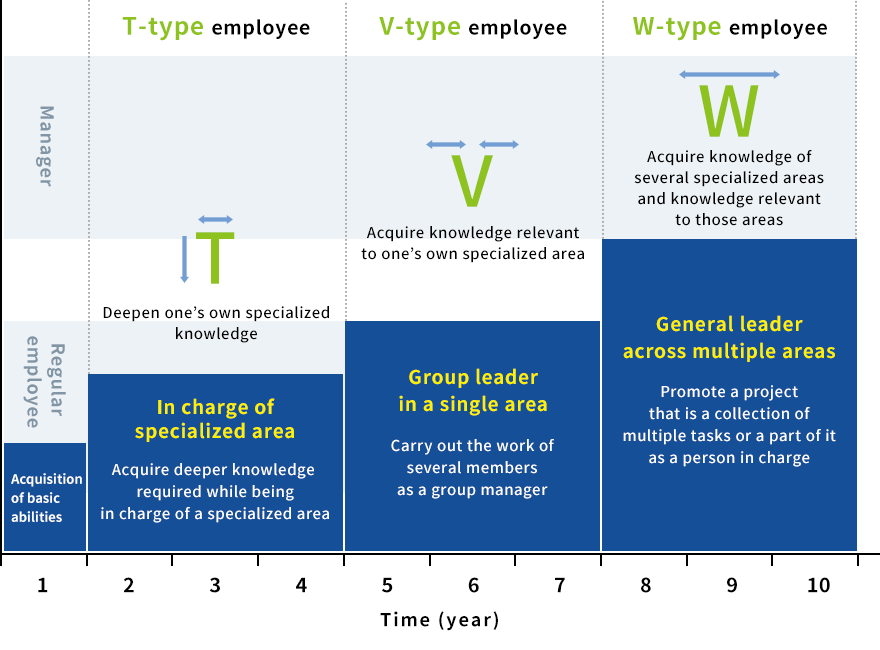
FAQs
Here we answer some of the most frequently asked questions about our HR recruitment.
-
Can I apply for a position without any experience?
Yes, you can.
-
Is there a training period after joining the company?
No, there is no training period.
You will acquire practical knowledge and skills in the field through OJT.
You will be surrounded by experienced seniors and colleagues, so you can always ask them about anything you don't understand. -
Is it possible to adjust the joining date?
Yes, you can.
Inquiry by phone or email
If you have any questions regarding recruitment, please contact us at the Recruitment Team, Personnel Section, Human Resources Department, Nissin Manufacturing. Call the phone number below or send us an email by clicking on the link below.
Tel: +81-772-62-1111
(Not necessary to translate)