
Medical Division
(Medical Device Business)
Based on the sound manufacturing system we have cultivated through the development and manufacturing of automobile engine parts and machine tools, we are currently engaged in research and development of medical devices that contribute to advanced medical care. We will establish the medical business as a next-generation business pillar of the Nissin Manufacturing Group and thereby contribute to the future of medical care.
Our goal is to achieve innovative manufacturing that creates a new category in the industry
We are conducting research and development through industry-academia collaboration toward the realization of a fracture treatment support system that is being built by the Department of Orthopaedic Surgery, Shimane University School of Medicine. This is an innovative attempt to create bone screws used in fracture treatment from the patient's own bone. Nissin Manufacturing works on the development of a multifunctional bone processing machine to create bone screws that join a fractured bone by applying its industrial technology, which is used to create complex three-dimensional shapes through cutting, in the medical field.
Our goal is to create medical devices in a new field that not only have excellent processing accuracy and safety performance but also an intuitive user interface that allows doctors to operate them without hesitation during surgery. We put our heart and soul into developing innovative products that create a new category in the medical device industry.
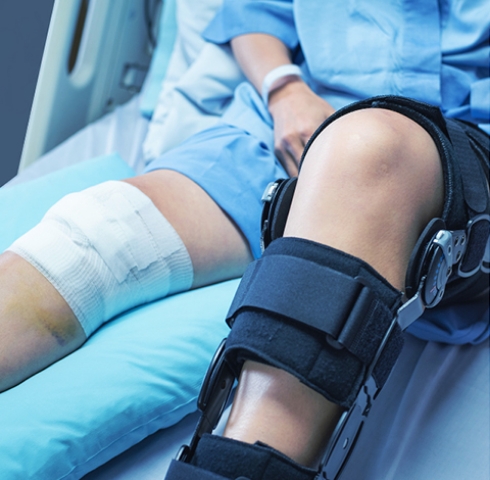
Nissin Manufacturing as a medical device manufacturer
The Medical Division is engaged in the development of medical systems that encompass not only parts manufacturing and software development but also everything from design, development, manufacturing to operation. The company is now in the position of becoming a completely independent manufacturer of medical devices
Medical device manufacturers are required to strictly adhere to standards and rules and ensure maximum safety, making it difficult for manufacturers in other industries to enter the market. However, we will overcome this high hurdle with an uncompromising manufacturing system that is rooted in Nissin Manufacturing. We aim to become a medical device manufacturer that provides reliable and safe systems based on a solid development and manufacturing system that continually improves and an advanced quality assurance system that has accumulated a track record as a Tier 1 supplier in the automobile industry.
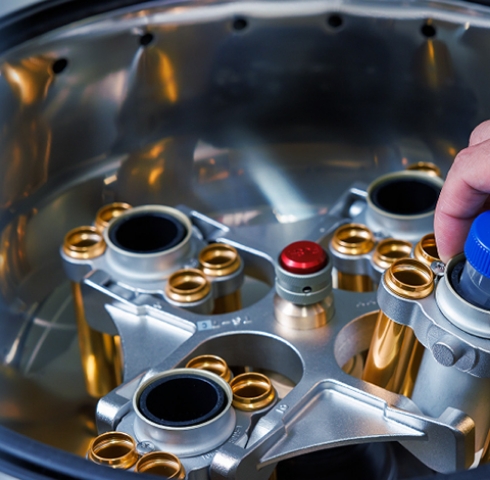
Offering from Japan to the world
medical devices that can help 7 billion people
Going forward, we aim to develop the medical business into the second business pillar of the Nissin Manufacturing Group by 2030. The first step is the completion of a multifunctional bone processing machine. If this trial comes to fruition, people who have been unable to move their legs because of intractable fractures will be able to walk again, injured athletes will be able to perform at their best again, and children with potential will not have to give up on their futures. Such a new future will open up.
After building a foundation in Japan, we are thinking of expanding overseas. First, we plan to expand to the United States, which is the center of medical science and which can be said to have established the global standard for medical care, and then further to Asia. What the Medical Division aims for in the future is to help solve the problems of patients around the world with the medical devices we develop.
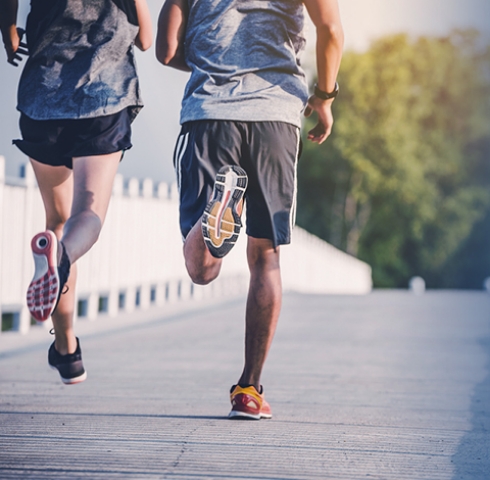
Technical Information
Nissin FULFIL’s development is based on
compliance with the strict QMS requirements
for medical devices.
Furthermore, by integrating six technological
fields, the company is taking on the challenge
of creating new medical devices that have
not yet existed in this world.
To achieve this, we are promoting efficient
development by coordinating technological and
regulatory strategies in a well-balanced manner
to enhance safety and efficacy.
We will create products that will leave
a mark on the history of medicine by combining
manufacturing technologies while adhering to
QMS requirements.
Mechanism design
We design the structure of parts that operate inside machines, using actuators such as motors. Based on technology for realizing high speed and high precision, which we have cultivated in the industrial field, we will overcome numerous challenges to develop a safe and reliable technology that can be used for medical purposes and thereby expand into the medical device field.
- 5-axis position accuracy control design
- By accurately configuring right angles and parallels and designing to ensure spatial coordinates, we are capable of achieving origin and position controls on a micron order and enabling 5-axis precision machining that requires highly accurate positioning. Through this technology, we aim to achieve precision that is suitable for medical environments that require fine control.
- Power control design
- In order to accurately transmit the power required for precision machining, we control backlash and lost motion, reduce inertia during acceleration and deceleration, and thereby perform control designs that aim to reduce power transmission losses and improve precision. In addition, we minimize risks through risk management to enable the development of highly reliable medical devices.
- Machining and automation designs
- To ensure stability of machining accuracy, it is important not only to control positioning accuracy on a micron order but also to design with machining axis rigidity in mind. By selecting optimal materials, designing parts that increase the rigidity of the machined sections, and introducing ATC equipment, we realize machining and automation designs that ensure light weight and high rigidity.
- Simulation and analysis
- We perform strength calculations and fluid analysis through structural analysis by introducing various simulation technologies. We identify issues and make repeated improvements on 3D design data, which lead to a reduction in the number of prototypes and improved prototype accuracy. Furthermore, we use 3D design data to find indicators to guarantee the reliability and safety of equipment and reflect them in the design.
Structural design
We work on equipment design with the aim of developing equipment that combines safety and design. We select materials for the parts of the entire product, arrange the parts, and design the housing to create the product from scratch. After prototyping, we verify the design and function with an aim to further improve operability and functionality.
- Functional arrangement
- We improve the operability and functionality of the entire device by considering a functional layout that allows medical personnel to operate it comfortably without making mistakes. We also take into consideration how to ensure cleanliness, which is an essential requirement for a medical device. In particular, we achieve an exceptionally high level of cleanliness for the sections that come into contact with the affected area of the patient. In this way, we conduct design studies that thoroughly ensure safety while pursuing usability.
- Housing design
- The top priority in designing the housing of a medical device is safety. Since we are working on the design of pioneering equipment, we select parts, design parts, and produce prototypes based on required specifications only after thoroughly identifying possible risks through risk management and formulating countermeasures in advance. After producing a prototype, we repeatedly evaluate and improve it to create a product that will be useful to a wide range of people.
Electrical circuit design
To produce control boards, we design analog and digital circuits that match the system. We also design wire harnesses to connect control boards to the peripheral hardware of the system. We perform electrical safety evaluations to ensure problem-free operation in clinical settings and work with engineers from other fields to ensure compliance with EMC standards.
- Circuit design
- We design analog and digital circuits. We use electrical CAD to design circuits, including those to control motors and mechanical parts that operate with high precision, and sensor circuits to control and monitor the internal conditions of medical devices and disposable products. We ensure safety in accordance with the medical standard IEC60601-1 and conduct design verification and validation testing.
- Wire harness design
- We design wire harnesses to connect circuit boards and peripheral hardware. In addition to selecting cables according to the voltage, current, and surrounding environment, we also take measures to increase noise resistance to prevent malfunctions and effects on peripheral devices. Furthermore, in order to prevent incorrect assembly, we take the manufacturing process into account in designing and improve the quality of the equipment.
- Electromagnetic Compatibility (EMC)
- We perform EMS and EMI testing to confirm compliance with EMC requirements. If a defect is confirmed, we will work with the manufacturer and those in charge of mechanism and software design to formulate optimal countermeasures from both hardware and software perspectives. We aim to develop medical devices that strictly comply with IEC60601-1-2 by having engineers specializing in various fields work together to solve problems.
Application/system design
We perform application design and system control design using multiple programming languages, such as C, C#, and NC. Meantime, we conduct usability design, real-time design that aims to achieve advanced control, and software testing to ensure the high level of safety required in medical settings.
- User interface design
- We design interfaces with human factors in mind. In order to prevent information misunderstandings and incorrect operations in medical settings, we perform design to enhance visibility and operability, using assumed usage scenarios and feedback collected across departments. Furthermore, we ask actual doctors who will be the users to try out a mockup of the device, and we continue to make improvements based on a wide range of opinions from those doctors.
- OS control
- Since a system is constructed using a large amount of hardware, efficient hardware control and high responsiveness are required when multiple tasks occur. Accordingly, we perform real-time control, using the OS to manage task priorities. Additionally, since an OS is software that has vulnerabilities, we perform designing with security in mind while assessing its validity and safety.
Embedded software design
The role of software design, which is located downstream in the equipment development process, is to breathe life into the designed equipment so that it operates as expected. We design software for microcomputer control of peripheral hardware and ICs on boards by using mainly assembler and C language.
- Hardware control
- In order to accurately and safely control a medical device that is connected with a variety of instruments, including motors, sensors, memory ICs, and other extremely small electronic instruments, it is essential to have accurate understanding of the characteristics of all instruments. We thoroughly read data sheets and accurately understand the operation of each instrument before starting the development of software that controls the entirety of a medical device.
- Real-time design
- To ensure that a medical device operates safely and reliably, each instrument that makes up the device must operate in a timely manner. We design tasks and memory by understanding the characteristics of each instrument and solving problems, such as noise, one by one to enable advanced and precise real-time control.
Quality assurance
With the goal of ensuring that our products operate without problems in medical settings and they benefit the health of many people, we evaluate and confirm, before and after shipping, whether they meet customer requirements and there are any safety issues. We also aim to maintain and improve quality by evaluating product reliability and controlling supplier quality.
- Reliability evaluation
- To prevent medical devices from causing misdiagnosis or treatment errors, we conduct thorough reliability evaluations from the early stages of design and development based on QMS, which leads to ensuring and improving the quality, effectiveness, and safety of medical devices To this end, we select and introduce appropriate evaluation/measuring instruments and equipment and thoroughly manage them to ensure that accurate evaluation results are always obtained.
- Post-market safety
- The development of medical devices that affect human life requires speedy responses to problems. To enable this, we collect market information early and analyze causes. If necessary, we take corrective measures in cooperation with each technical department and link them to preventive measures. By taking these steps in a timely and accurate manner, we aim to further improve the quality of our products.
- Supplier quality control
- Based on QMS, we confirm whether devices supplied by all suppliers involved in the development of equipment comply with established inspection standards and methods. Additionally, we are strengthening our quality control system in collaboration with our suppliers, constantly promoting the maintenance and improvement of the quality level of all parts used in our products.